Prevent, Protect and React
Network resilience is critical all year round, but never more so than in the winter months, Siemens' Mark Simblett tells Network - and transformers have a critical role to play.
14th February 2017 by Networks

Network operators are continually striving to make their networks more resilient. How important is the role transformers play?
Transformers are a key component when it comes to power transmission and distribution. They are placed at the critical nodes of electricity networks and make sure the power, which is generated in one spot is “sent” without major losses to where it is needed. Network operators create more resiliency by keeping spares, which can be quickly installed when failures happen.
What is the likelihood of failure in the UK’s transformer asset base?
The average lifespan of power transformers in the UK is probably between 30-40 years old if we average the asset base across the country. The technology does age, so a number of those are due for replacement. There are not a lot of moving components in a transformer but as they get older and we experience increased network capacity, they are worked harder. There is also an ageing process internally which can increase the likelihood of failures during normal and extreme operational situations.
Failure does happen. There have been a number of emergency projects in the past 12 months where transformers have failed and the customer has turned to Siemens for urgent support. These failures haven’t been linked to resilience, but like-for-like replacements, where utility companies have an asset management programme where they have spares and we have gone in and repaired or replaced them.
From our experience gained from being a partner of utilities worldwide for more than 100 years, Siemens knows about the condition of the grid in a lot of regions. To address concerns of the perceived increase of risk of transformer outages, we have created a modular three-step transformer concept called Pretact.
The first layer to reduce risks to the existing transformer fleet is called PREVENT. This includes several service modules, like condition monitoring, repairs and retrofit to prevent unplanned outages due to failures in operation. This usually gives the utility companies some breathing space to think about what it is they are going to do about that problem asset and whether to put in some other form of flexibility in the network.
The second layer consists of features to PROTECT the transformer from external risks. This may be extreme weather events like geomagnetic solar flares and thunderstorms, but also human impacts like vandalism. Some of these preventative features can be retrofitted, others need to be considered already when ordering a new unit.
The third and final layer is REACT, a fast moving mobile resilience transformer solution that enables transformer operators to replace the asset in a very short space of time.
How much does the risk of failure increase due to bad weather?
Transformers are quite robust machines, so it really takes extreme weather events to threaten their operation. However, the likelihood of extreme weather has risen during the past decade. In the UK we can have as much of an issue with wet weather in September as we do with snow in February. In addition, we need to look at the complete system and not only the transformer: if there is a failure in another crucial component this might lead to a transformer failure.
Looking at the recent past, thunderstorms and floods were the most common weather events that led to large blackouts in Europe. But, as mentioned before, not only weather is a threat to transformer operation. Events like vandalism and, less so here in the UK, earthquakes can also have tremendous effect. And, as always, the most spectacular risks are feared most, but the majority of transformer failures happen simply during operation because of an aged transformer fleet.
Siemens has created a solution that will cut replacement times in the event that assets do fail, how did this solution come into being?
Yes, if all precautions that utilities can take fail, Siemens has come up with an innovative transformer in their mobile resilience unit. It enables transformer operators to react quickly if the worst case scenario is inevitable.
The mobile resilience unit can be transported quickly to any location needed, because their single-phase design makes them compact and lightweight. The installation time is reduced dramatically, by up to 75%, because the units are equipped with plug-in-bushings and connections. This means the transformer operator can restore their system within a few days, rather than a period of weeks if a conventional power transformer was used. And, to top these advantages, mobile resilience units are built to fit different voltage levels. This means the transformer operator does not need to invest in several different units, but can backup different strategic nodes in the network with just one set of mobile resilience units.
Siemens is a pioneer in innovation. We are market leaders on innovation in the transformer business, but we don’t do that on our own. A significant part of our job is to listen to the concerns of our customers and find solutions to make their life easier. Our transformer resilience concept was incubated with a customer. It wasn’t just a product that we thought about and then just took it to market, it was actually generated with the customer in mind.
We are seeing increased amounts of decentralised generation now, and despite all the positives, this is challenging the current grid. That challenge can cause problems to transformers, particularly in regard to internal stress. Our resilience transformers have also been designed specially to address this.
What’s next in the evolutionary journey for transformers?
Environmental factors are a big driver for Siemens – recently rated #1 in the list of 100 Most Sustainable Corporations globally according to Corporate Knights. There are many environmental challenges when you are using a transformer that contains mineral oil, and we have worked hard to provide an alternative solution. In 2016, we manufactured the first transformer at 400kV for a project at Highbury substation with National Grid that is filled with an environmentally friendly ester-based product.
This adds to the resilience of transformers: replacing mineral oil filled units by esters adds to the operational safety of transformers as they have a higher flame- and flashpoint than mineral oil and thus do not burn as easily. Additionally this measure can have technical benefits as esters can add to a longer transformer lifetime or enhance the performance of transformers by allowing higher operational temperatures.
Comments
Login on register to comment
Related content
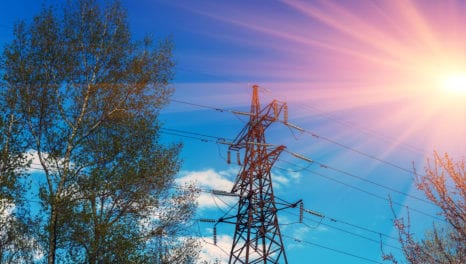
Power
The future for vegetation management
Why networks should focus on data not trees to overcome the costly challenges involved in vegetation management
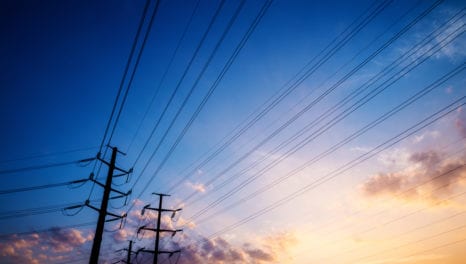
Power
An unprecedented opportunity for change
Why short interruptions will matter in RIIO-ED2 and how to address them.
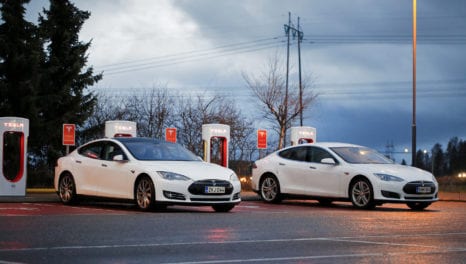
Power
Time for less talk and more action on decarbonisation
Core "oven-ready" solutions to decarbonising heat and transport exist today and should be implemented without delay, says WPD's future power networks expert.
Related supplier content
![‘Learning by doing’ on the road to net zero [test product]](https://networksonline.s3.amazonaws.com/products/images/3.jpg)
People & Skills
‘Learning by doing’ on the road to net zero [test product]
DSO director Andrew Roper discusses 'Learning by doing'

Power
Load patterns and lockdown: how Covid-19 is impacting electricity networks
Insights into dynamics on the low voltage network as the outbreak unfolds
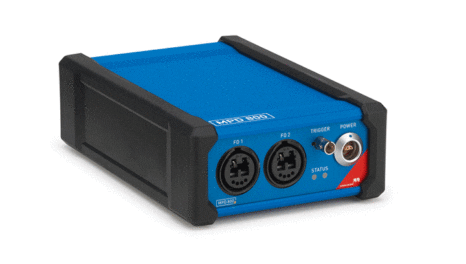
Downloads
Protect electrical equipment from insulation failure
Insulation faults are a major cause leading to the eventual failure of electrical equipment. Partial discharge (PD) is a very reliable indicator of developing insulation faults. Regular PD testing allows users to detect and analyze PD activity